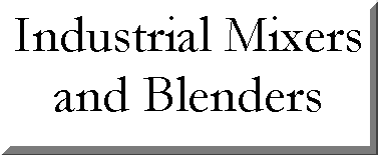
For over a century Kelly Duplex
has been manufacturing industrial processing and material handling
machinery to handle a wide range of materials and applications for
industrial processes. We have specialized in building heavy duty,
trouble-free machines to meet our customer’s individual needs. Our goal
is not to sell a new machine to replace a 5-7 year old machine, but to
install a new unit next to the original one.
As
our customers grow, we grow.
This broad experience has not
been limited to a few types of machinery – or a few models. For example,
we build a variety of distinctly different types of industrial mixing
equipment. All are constructed to give you top performance and long life
under maximum production conditions. All are customized and available in a
wide range of capacities, and throughputs. All are built to meet our own
rigid safety standards.
In the broadest terms we
build mixers and blenders for continuous or batch operations. These mixers
may be handling a very small batch of chemicals in a laboratory, bulk
complete trailer loads of plastic, or adding water to ash in a foundry.
With our experience and design expertise we can manufacture mixers and
blenders to meet just about any customer’s application.
We also offer a variety of
mixing actions for both batch and continuous operations. We can design
mixers and blenders to gently handle products, or to very aggressively
apply shear for high energy mixing dispersion.
In addition to our mixers
& blenders we also manufacture a compete line of complimentary
material handling equipment.
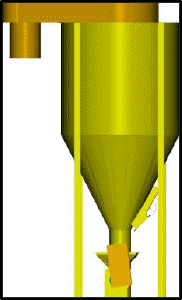

Horizontal
Mixers
The
Kelly Duplex Horizontal Mixer is unsurpassed for fast, thorough, accurate
blending, heavy duty construction, long life, and trouble free
performance. Curved, adjustable paddle blades combine a scooping and
lifting action with a unique “criss-cross” blending pattern to assure
that all material is continuously overlapped and blended to obtain a
completely uniform product throughout the batch. This blending action
provides the turbulent upward and downward movement required to blend
liquids with solids, yet is gentle enough that such delicate materials as
granular chemicals or rolled grains can be mixed without destroying the
flake or texture. This unique Kelly Duplex action assures rapid mixing,
leaves no pockets, lets you blend materials with widely varying densities,
mixes micro ingredients with large amounts of basic ingredients, provides
for a thorough cleanout and positive discharge. The mixer uniformly blends
partial batches as easily and completely as it does full batches.
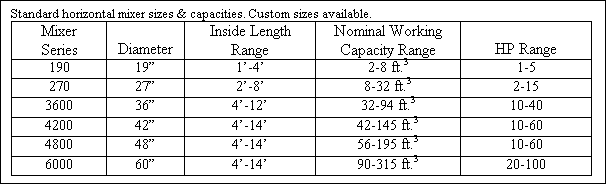

Continuous Mixers
Kelly Duplex Continuous Mixers are unsurpassed for fast,
thorough, continuous stream blending. For well over 50 years Kelly Duplex
has been consistently building a reputation for rugged, accurate, and
economical continuous mixers. Our continuous mixers are ideally suited for
an almost limitless variety of solid-to-solid and liquid-to-solid
continuous stream mixing jobs. Typical capacities range from 50 ft.3
– 12,000 ft.3 / hour. There is an almost unlimited number of
options available for these mixers, like all of our mixers; customized
spray manifolds, access panels, customized mixing tool combinations, and
of course sizing to meet unique customer requirements. Whatever the
continuous mixing requirement, we’re confident we can meet it.
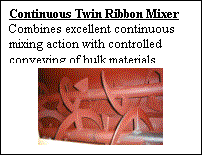
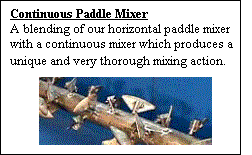

Vertical Mixers
Kelly
Duplex Vertical Mixers are designed for fast, thorough blending of free
flowing granular or fine materials. Typical mixers can handle batch sizes
from 10 ft.3 to 1800 ft.3. Large batch volumes are
possible at a low initial cost with low horsepower requirements when
compared with traditional (horizontal) type mixers. Excellent and rapid
mixing action is provided by a large vertical helicoid screw spiral
partially enclosed in an internal tube. Free flowing materials are
elevated to the top of the mixer vessel where the product is mechanically
dispersed. Mixing takes place by combining gravity flow, top dispersion,
and bottom agitation in the lower conical area of the body. This mixer is
especially well suited to applications requiring extra large batch sizes,
where floor space is limited, or where a self-loading, self-discharging
agitated storage vessel is required
